In the quest for greater efficiency and environmental responsibility, industrial processes must continuously evolve. One transformative approach involves leveraging the power of waste heat to optimize industrial drying processes. Waste heat, often seen as an unused byproduct of various industrial operations, can be repurposed to fuel drying systems, offering both economic and ecological benefits.
Defining Waste Heat
Waste heat, or excess heat, is the thermal energy generated during industrial processes that is not utilized and is often released into the environment. This energy is found in various forms, including hot exhaust gases, cooling water, and heat lost from equipment. Managing waste heat can be costly because it often requires additional energy to cool it down before it can be safely released. Instead of being discarded, this valuable resource can be harnessed to improve industrial operations.
At STELA Drying Technology, we view this so-called “waste” heat as a critical asset that can fuel our innovative low temperature drying technology, transforming what was once seen as waste into a powerful energy source.
The Benefits of Utilizing Waste Heat
- Reduced Reliance on Fossil Fuels: By capturing and utilizing waste heat, businesses can significantly reduce their dependence on fossil fuels. This shift not only decreases operational costs but also supports environmental sustainability.
- Enhanced Energy Efficiency: Repurposing waste heat leads to higher overall energy efficiency. This improvement translates into substantial cost savings, making industrial processes more economically viable.
- Minimized Environmental Impact: Utilizing waste heat reduces greenhouse gas emissions and lowers the environmental footprint of industrial activities. This approach aligns with global efforts to promote cleaner production methods.
- Access to Grants and Incentives: Companies that invest in equipment to utilize waste heat may qualify for various monetary incentives, such as federal and state grants, tax credits, utility rebates, and low-interest loans. These financial benefits can help offset the capital investment costs, making it more attractive for businesses to adopt sustainable practices.
Case Example: Innovative Drying Solution for OSB Production at Swiss Krono
Swiss Krono, a leader in wood-based materials, faced a significant bottleneck at their Zary facility in Poland. Their existing dryer struggled to meet the demanding task of drying OSB strands from 50% to 2% moisture content, limiting production capacity and overall efficiency. STELA provided a solution by installing a BTU production capacity system that utilized waste heat from the resin plant. This innovative approach pre-dried strands before they entered the original dryer, increasing efficiency and production capacity while reducing reliance on fossil fuels and operating costs. To read the full Swiss Krono case study, click here.
Conclusion: Rethinking Waste Heat – A Sustainable Advantage
Industrial processes often generate significant waste heat, a valuable resource that has traditionally been overlooked. By capturing and utilizing this thermal energy, businesses can unlock a wealth of benefits. STELA’s innovative drying technology treats waste heat not as a byproduct, but as a strategic asset.
Our low-temperature drying solutions effectively transform waste heat into a powerful tool for optimizing industrial drying processes. This approach translates to greater efficiency, reduced reliance on fossil fuels, and a minimized environmental footprint. The result? Sustainable industrial practices that benefit your bottom line and reduce your CO2 footprint.
Ready to unlock the potential of waste heat to fuel your drying process? Contact STELA today to learn how our innovative solutions can help you achieve a more sustainable and efficient future.
Practical Applications
Waste heat can be found in numerous industrial settings, from power plants to manufacturing facilities, and can be repurposed to enhance energy efficiency and sustainability. This resource can be harnessed in various industries, such as the cement industry, biochar production, and for energy recovery and low-temperature drying applications. Here’s how it works:
- Cement Industry: Traditionally, cement production relies heavily on fossil fuels, significantly contributing to CO2 emissions. Advanced drying technologies, like those from STELA, capture excess heat from downstream processes such as hot air from clinker cooling. This captured heat is then adjusted to a suitable temperature for drying raw materials, transforming alternative fuels like Refuse Derived Fuel (RDF) and Municipal Solid Waste (MSW) into valuable resources. This not only reduces CO2 emissions but also boosts sustainability in the cement industry.
- Biochar Production: Processes that convert organic materials into valuable products like biochar and syngas require both cooling and drying stages. Waste heat can be used to efficiently manage these stages, enhancing the overall efficiency and sustainability of these processes. By repurposing waste heat, these technologies can operate more effectively, reducing energy consumption and environmental impact.
- Energy Recovery and Low-Temperature Drying with Waste Heat: Waste heat generated by Organic Rankine Cycle (ORC) or combined heat and power (CHP) systems can be a valuable resource for low-temperature drying applications. However, successful integration depends on the specific temperature and volume of the available waste heat. When conditions are optimal, utilizing waste heat for drying can be highly beneficial. This approach maximizes overall energy utilization and minimizes CO2 emissions, perfectly aligning with the modular and efficient nature of low-temperature dryers.
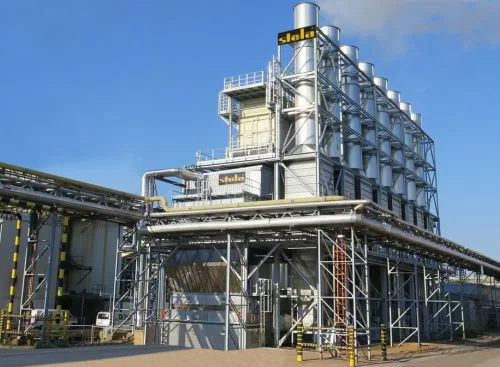