Challenge:
The SCHWENK cement plant in Allmendingen prioritized the efficient utilization of previously unused waste heat from the production process. Recovering this thermal energy – which would otherwise dissipate into the environment – offered a unique opportunity to drive operational efficiency, reduce reliance on external energy sources, and advance the company’s broader sustainability goals.
The site presented a significant constraint: limited available space. Although a belt width of 20.3 feet (6.2 meters) had proven highly effective at other SCHWENK locations, integrating this size dryer within the existing infrastructure at Allmendingen required a complete redesign. SCHWENK once again selected a STELA low-temperature belt drying system – specifically, the STELA BT 1-6200-13.5 model—based on strong performance at other sites.
Solution:
STELA developed a custom installation to address the space challenges. The exhaust air fans were placed behind the dryer and connected with ducts routed beneath the belt system – an unconventional layout that enabled full integration despite the tight footprint. The belt dryer was also constructed on an elevated 6.6-foot (2-meter) strip foundation to accommodate the customer’s essential infrastructure.
The system harnesses waste heat from the clinker cooler, previously lost to the environment, to dry the RDF material. The dried RDF, largely composed of shredded plastics, serves as a lower-emission alternative to coal for the rotary kiln. This approach not only improved the plant’s energy efficiency but also significantly reduced its carbon footprint.
STELA’s modular belt dryer design proved key to success, offering a flexible and scalable solution for constrained industrial environments. Additionally, the integration of RDF drying with clinker cooler waste heat enhances fuel flexibility, reduces reliance on auxiliary fuels, and supports combustion stability in the kiln.
Result:
The project at Allmendingen stands as a model of engineering innovation under challenging conditions. The STELA belt dryer now enables SCHWENK to recover valuable waste heat, optimize substitute fuel use, and meet rigorous operational and environmental targets.
Assembly was completed in close coordination with SCHWENK, with special attention to site conditions and existing energy systems. Thanks to meticulous planning and cross-functional project management, the dryer installation proceeded on schedule, providing valuable insights for future retrofit projects where space limitations are a critical factor.
The system now saves more than 29.0 million BTU (8.5 million kWh) of energy annually and avoids over 14,550 short tons (13,200 metric tons) of CO₂ emissions – delivering meaningful progress toward SCHWENK’s sustainability goals.
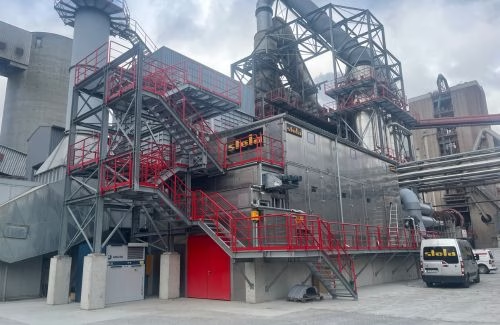
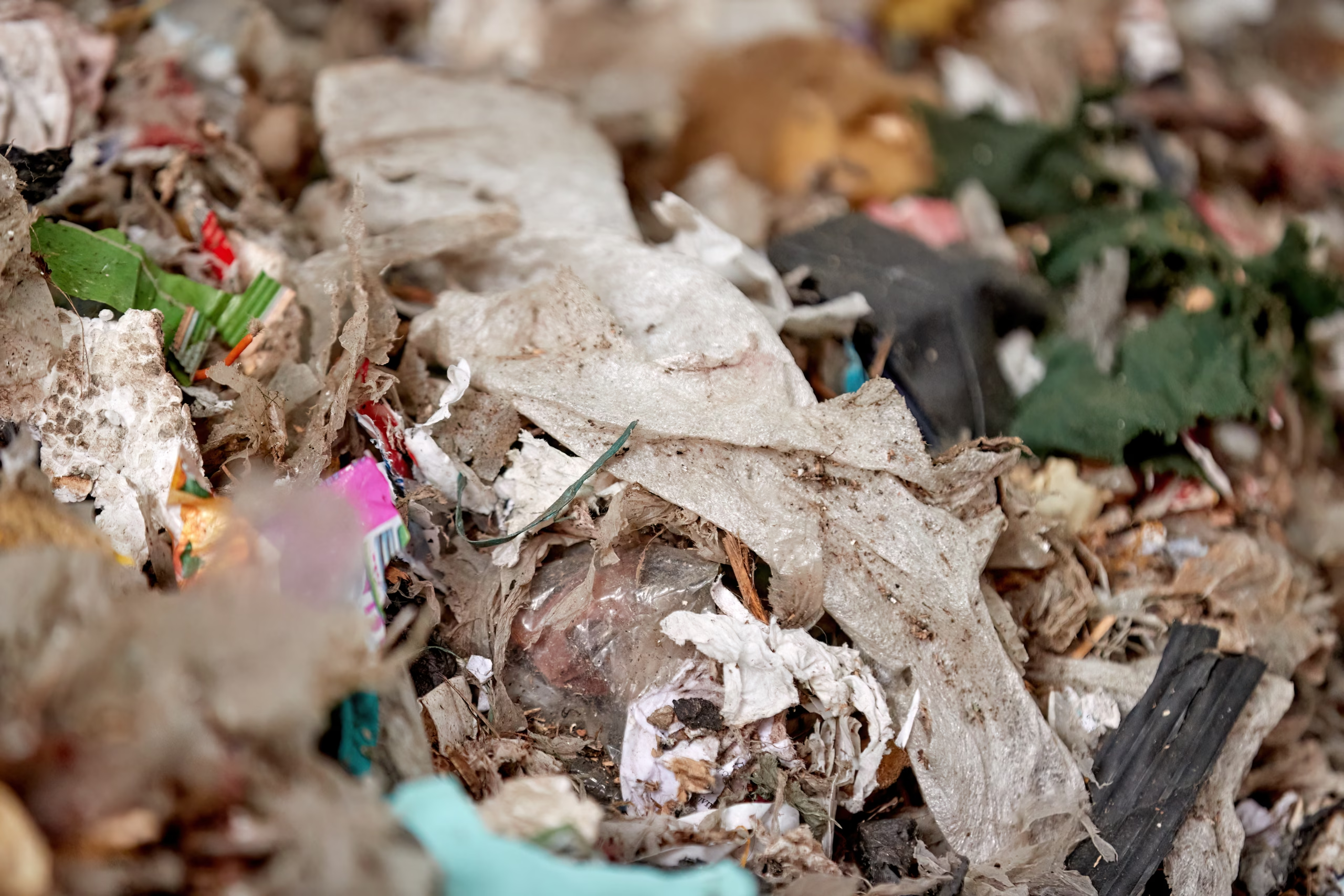
Conclusion:
The Allmendingen project demonstrates the power of low-temperature belt drying technology to drive both efficiency and environmental performance. By leveraging STELA’s flexible drying solutions, SCHWENK achieved a high-impact operational upgrade that supports decarbonization, energy recovery, and circular economy goals.
This case study underscores STELA’s role as a partner for future-ready industrial solutions, enabling plants like SCHWENK Zement to meet the evolving demands of sustainability and operational excellence.
About SCHWENK Zement:
Founded in 1847, SCHWENK Zement is one of Germany’s leading producers of high-quality cement and building materials. With a strong commitment to innovation, efficiency, and environmental responsibility, SCHWENK operates multiple state-of-the-art facilities across Europe, delivering essential materials for infrastructure, housing, and industry.